Rice milling industry is one of the most energy consuming industries. A rice mill consumes energy forms in terms of water, air, steam, electricity, and labor. In a rice mill, some of the operations are done manually namely, cleaning, sun drying, feeding paddy to the bucket elevators, weighing and packaging, etc. While water is employed for soaking and steam generation, it is Electricity the guzzler being the main energy source for these rice mills. Electricity is also used to operate motors, pumps, blowers, conveyors, fans, lights, etc.
The variation in the consumption rate of energy through the use of utilities during processing is a huge factor of production for the final cost of the finished product. Through ongoing efforts have yielded results, only a few have radically improved their energy efficiency levels. Old locally available technologies and incompetent, the absence of technical training in available technical personnel are some of the root causes. 
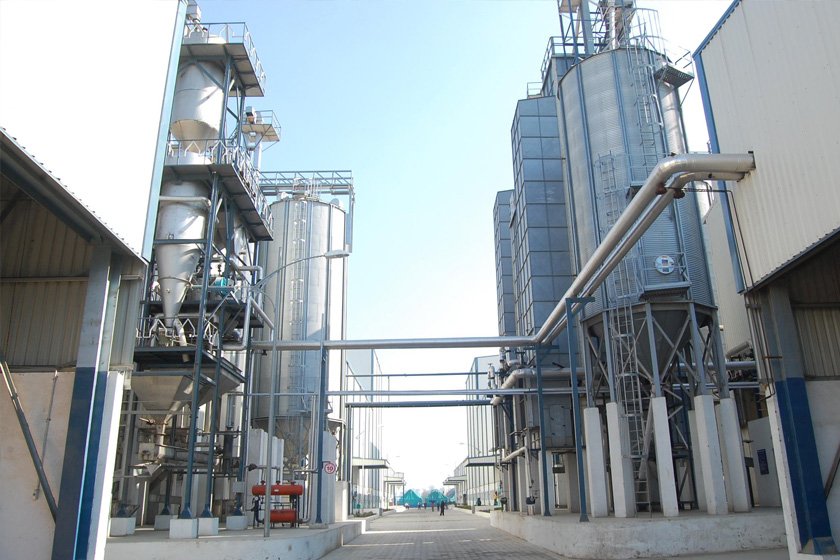
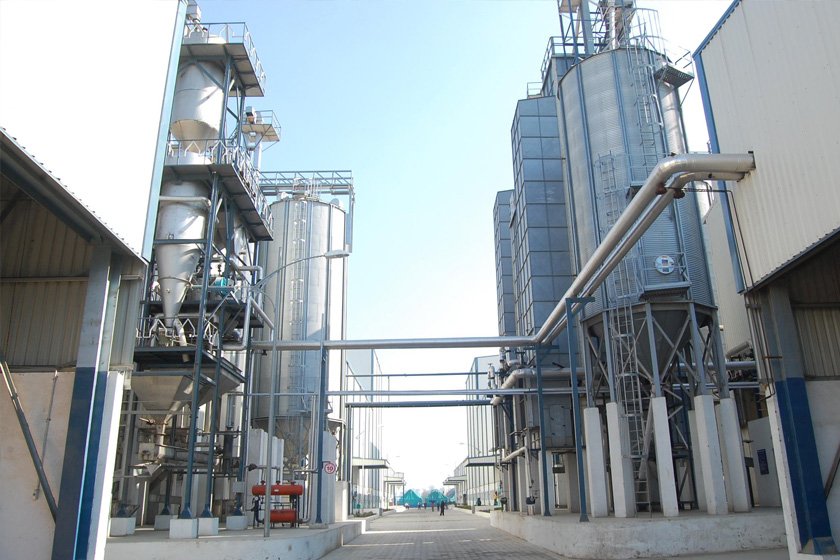
Consumers and regulators today are becoming stringent about environmental issues such as pollution and global warming. Existing Rice mill plant & upcoming rice mill projects located anywhere in the world have realized the need for rice mill solutions that act proactively & that outline macro as well as detailed policy for evolving energy concept in order to ensure energy-savings and green practices. These enable the processes to be both cost-effective and environmentally friendly and enable greater returns.
SOME SUSTAINABLE ENERGY SOLUTIONS FOR RICE MILL PLANT
Few Rice Mill Project Consultants and even some Rice Mill Engineers & Designers are offering services like energy audit, executing energy saving processes and equipment, employing renewable energy for energy cost reductions as well risk reduction against energy hazards. Transparent processes are being implemented to allow knowing electrical safety measures, energy consumption patterns, energy wastage in each process, & if energy savings are possible and the what-if scenarios to calculate the project cost vis a vis savings payback.
One of the greatest sustainable measures is to effectively employ and monetize wastage for creating useful products. Rice being a nature’s bounty- offers many uses even after the main kernel has been removed.
The two most important waste to use products are Rice bran oil & biogas from rice husk. Rice bran is perhaps the healthiest cooking medium with an ideal balance of polyunsaturated fats (PUFA) and monounsaturated fats (MUFA). Rice bran oil is made from bran and is rich in Vitamin E and makes for an excellent antioxidant.
It has been used in the edible oil industry for quite some time. Rice husk is one of the by-products of rice processing has a high combustion value (75%) and high calorific value. This makes for an easily available, convenient and cheap renewable energy source. As Rice husk has also a small bulk density making it easy to transport, it is a convenient fuel for the biomass/rice husk power generation system. Many mills now recycle rice husks to greatly reducing the operating cost, increase operation efficiency and achieve greater returns from the rice milling plant.